Compression molding of composites pdf
SPORTING GOODS – SNOWBOARDS / SURFBOARDS ReRez® Epoxy Resin E2930 with ReRez® R2107 Curing Agent is specifically formulated for heat assisted curing, compression molding applications, such as for skis and snowboard manufacturing.
About Compression Molding High pressure thermoset molding process where a complete molding compound, which includes resin, reinforcement, colorant and any other required additives is weighed out precisely and placed in a heated mold cavity, pressure is applied to force the molding compound to evenly fill the mold.
During compression molding of glass ber reinforced plastic composites, annealing and quenching experiment is conducted by changing pre-heating and cooling method. As results, major cause of unevenness that a ects
Green Composite Manufacturing via Compression Molding and Thermoforming. Birat KC, Muhammad Pervaiz, Omar Faruk, Jimi Tjong, Mohini Sain . Pages 45-63. PDF. Compaction, Permeability and Flow Simulation for Liquid Composite Moulding of Natural Fibre Composites. Darshil U. Shah, Mike J. Clifford. Pages 65-99. PDF. Manufacturing and Processing of Kenaf Fibre-Reinforced Epoxy Composites …
Compression molding of composite materials yields a superior surface finish and good dimensional stability between component lots with faster processing compared to traditional manufacturing methods. This experimental compression molding capability was developed for the ME composites lab using unidirectional carbon fiber prepreg composites. A direct comparison was drawn between autoclave …
In this paper, the insulating composites which consist of polyester fiber wastes and PLA films are molded by compression molding method. In the process of preforming, the polyester fiber wastes are arrayed in uni-direction, and PLA films are inserted among layers of the polyester fiber wastes as binder. Namely, the polyester fiber wastes layers and PLA films are laminated alternately. In this
Fabrication of Composites: According to Garkhail et al., (1999), compression Injection molding and extrusion are the more molding produces composites with better mechanical popular methods of fabricating PLA composites. properties when compared with composites This research has contributed to the possibility of fabricated using injection molding. In this study, the using compression molding …
A tool for compression molding a composite laminate charge has a tool face for compressing the charge. A flexible tool feature on the tool face forms a shape in the charge and compensates for tool surfaces that may be out-of-tolerance.
Read “Simulation of compression molding for sheet molding compound considering the anisotropic effect, Polymer Composites” on DeepDyve, the largest online rental service for scholarly research with thousands of academic publications available at your fingertips.
Download the PDF brochure for more information about TenCate’s compression molded composite solutions. TenCate Advanced Composites specializes in designing and developing advanced composite materials for the industrial, aerospace, satellite and …
Compression Molding of SMC (sheet molding compound ) This molding technique involves compressing material containing a temperature-activated catalyst in a heated match metal die using a vertical press. The matched metal dies define the outer surface of the part being made. The molding process begins with the delivery of high viscosity uncured composite material to the mold. Mold …
Comoldco Corporation composites and insulators: At Comoldco we specialize in thermoset compression molding of FRP plastics and thermal/acoustic attenuation materials for automotive and a diverse range of markets.
Compression molding uses heated steel tooling in high pressure presses to produce more complex, high volume parts with fast cycle times. Compression molding is a high volume molding method that yields fast cycle times, high part uniformity, and allows for …
in a composite material must adhere well at the interface. In all-cellulose composites, where the In all-cellulose composites, where the components are made of …
Compression Molding Composites One

What is Compression Molding? TranPak
The Magazin of the Business Unit Composites Issue 2015 CFRP – LFT – SMC – Hybrid Lightweight Strategy for the Automotive Industry Page 4 Composites. Interview with Dr. Florian Luginger Page 4 Lightweight Strategy for the Automotive Industry Wet Molding Method Page 8 An Economical Alternative to Mass Production of CFRP Components Carbon for Large Scale Production Page 10 …
Compression molding creates structural components for modern aircraft interiors, replacing aluminum for weight and cost savings. In more demanding applications, such as the CFM Int’l. LEAP engines powering the A320neo and 737 MAX, composite fan blades are made in a compression molding …
Liquid Compression Molding (LCM) Technology for Mass Production of Continuous Fiber Composite Epoxy Matrix Components Stephen Greydanus, Cedric Ball, Ian Swentek– Hexion
compression molding, injection molding, and transfer molding. Matched die Matched die molding can be a wet process but it is most convenient to use a preformed molding
Characterization of Tapioca Residue and Coir Fiber as Reinforcement Foam Composites Obtained by Compression Molding Tarinee Nampitch1, a, Thiti Kaisone1, b*, Pran Hanthanon1, c, …
H. Suherman, A. B. Sulong, and J. Sahari, “Effect of the compression molding parameters on the in-plane and through-plane conductivity of carbon nanotubes/graphite/epoxy nanocomposites as bipolar plate material for a polymer electrolyte membrane fuel cell,” Ceram.
The Compression Molding workshop is a limited seating workshop hosted by CompositesWorld and IACMI. OEMs and composites fabricators will learn about existing technologies, specifically compression molding and HPRTM.
Compression molding, in addition to filament winding, lay-up and reaction injection molding processes, allows Advanced Composites Inc. to be almost unlimited in our ability to produce carbon, fiberglass and aramid composite structures for all applications.
.jpg)
Compression molding of long, discontinuous fiber, thermoplastic composites had been around since the 1990’s (Ref. 1) where fiberglass and polypropylene …
Compression molding of randomly oriented strands (ROS) of thermoplastic composite is a new process that enabled the formation of complex shapes with high fiber volume fraction.
The compression molding is an established and proven technique for the production of extensive and lightweight green composite materials. The advantages of this process are lightweight
Second, loose fibers were dispersed directly into the thermoset matrix to produce a bulk molding compound that was further compression molded into composite lamina. The effect of processing variables such as compaction pressure, temperature, and time were addressed. Moreover, the effect of fiber volume fraction
Continuous carbon fiber reinforced polypropylene was fabricated by the high-speed compression molding method, and the effect of maleic anhydride-modified polypropylene on the mechanical properties of CFRP was

Custom manufacturer of compression molded composites. Compression molding can be done from 30 to up to 750 tons. Composites worked with include wet and pre-impregnated resins (epoxy, polyester, phenolic, polyimide, and bismaleimide) combined with fiber reinforcements (e- and s-glass, aramid, carbon, graphite, quartz, polyethylene, copper, and
The demand for natural fiber composites in the automotive industry in both Europe and the United States has been forecasted to increase in the coming years. The natural fiber composites based on highly commercialized fibers such as flax, hemp, and sisal has grown to become an important sector of polymeric composites. However, little attention
Investigation into the Direct Compounding and Compression Molding of Glass Fiber Reinforced Polyamide 66 Composites”, Automotive Composites Consortium Technical Report, TR ACC932 -16. 5.
FABRICATION AND MECHANICAL PROPERTIES OF UNIDIRECTIONAL
A brief overview of various compression and injection-compression molding technologies for manufacturing of composites is presented. Important aspects involved in molding are considered, including molding schemes and various stages of processes, various compounds and ingredients used for their preparation, and compounding methods utilized.
The main advantage of compression molding is the ability to use any forms of natural fibers as reinforcements. An interesting advancement would be the use of braided natural fiber yarns produced by a process termed ‘micro-braiding’ for the fabrication of natural fiber composites.
This experimental compression molding capability was developed for the ME composites lab using unidirectional carbon fiber prepreg composites. A direct comparison was drawn between autoclave and compression molding methods to validate compression molding as an alternative manufacturing method in that lab. A method of manufacturing chopped fiber from existing unidirectional prepreg …
Compression molding for aerospace composites Features – Molding. Greenerd Press & Machine Co. expert Mike Josefiak explains how controlling temperature, pressure, and cure times improves consistency in critical composite materials.
Advanced Materials 2 Presentation Contents 1. Composites in mass production 2. Structural composite processing 3. Dynamic Fluid Compression Molding
unidirectional composites by compression molding. Silk fiber from local product of Surin province, Thailand was shown and PLA degrades at ~320 °C.
Molding composite structures under pressure. Compression molding is a closed-mold composite manufacturing process that uses matched metal molds with the application of external pressure. – html5 and css3 building responsive websites pdf Compression molding is the most common choice for high-volume composite parts and often associated with SMC and BMC materials. This process produces high strength, complex parts in …
Compression molding processes are widely used in the au- tomotive industry for high volume production capabilities and injection molding (qv) is adopted when the production rate is a critical issue, mainly for consumer
Compression Molding Capabilities Presses of various sizes with state of the art electronic controls to provide process stability, part conformance and repeatability. Materials Processed:
Introduction • Molding is the forming process . • Compression molding process is followed by two step first one preheating and pressurizing
Journal of composites science Article A Novel CAE Method for Compression Molding Simulation of Carbon Fiber-Reinforced Thermoplastic Composite Sheet Materials
Continuous compression molding (CCM) is a process used to fabricate thermoplastic composite (TPC) laminates in continuous lengths. One CCM process is described in German Patent Application DE 4017978 C2, published September 30, 1993 .
Molding conditions and the configuration of the elements for each board are shown in Table.1. To deliberate the effect of molding temperature gives to the mechanical property of the board, temperature was set to 110, 130, 150, 170, 190, 210, 230, 250 degrees Celsius. Board density was set to 0.8g/cm
1 SIMULATION OF THE COMPRESSION MOLDING OF UNIDIRECTIONAL COMPOSITE LEAF SPRINGS B. Gardarein 1, P. Durand2, P. Lory 1 1 Research Department, RENAULT
336 / OCTOBER 2014 INTERNATIONAL JOURNAL OF PRECISION ENGINEERING AND MANUFACTURING-GREEN TECHNOLOGY Vol. 1, No. 4 composite materials …
Compression molding is a well known technique to develop variety of composite products. It is a closed molding process with high pressure application. In this method, as shown in figure 1, two matched metal molds are used to fabricate composite product. In compression molder, base plate is stationary while upper plate is movable. Reinforcement and matrix are placed in the metallic mold …
carbon black-reinforced thermoplastic composites through compression-molding processing techniques for electrically conductive applications. Carbon black-based conductive composites produced by compression-molding processing techniques can be used in a wide range of applications in the structural and electrical areas. Selection of composite materials for the proper end-use …
Compression Molding. Compression molding is the process of molding in which a preheated polymer is placed into an open, heated mold cavity. The mold is then closed with a top plug and compressed in order to have the material contact all areas of the mold.
Compression molding is a high-volume, high-pressure method suitable for molding complex, high-strength fiberglass reinforcements. Advanced composite thermoplastics can also be compression molded with unidirectional tapes, woven fabrics, randomly oriented fiber mat or chopped strand.
The simplest molding process, hand lay-up is used in low-volume production of large products, e.g., wind turbine components, concrete forms and radomes. A pigmented gel coat is sprayed onto the mold for a high-quality surface. When the gel coat has cured, glass reinforcing mat and/or woven roving is placed in the mold, and the catalyzed resin is poured, brushed or sprayed on. Manual rolling
Aerospace Composites injection-moldings.com
The non-isothermal flow during compression molding of thermoplastic-based composites having a planar, randomly oriented fiber structure has been investigated.
the work is to investigate various properties of iPP/talc composites prepared by extrusion cum compression molding technique. With these aims, this research has been done and details of structural, physical and thermal
Compression or transfer molding of such platelets results in composite with complex meso-scale structure, which is semi- laminated and platelet level heterogeneous, to provide for sufficient
Compression molding process is the most preferred process as this addresses the problems of fiber damage effectively because of the minimal flow in the material. A brief study was done on the compression molded carbon composite parts in the industry. Identification of part manufacturers, process types, raw material suppliers are the key findings of the study. Compression molding …
Patrick Blanchard, Jeffrey S. Dahl and Daniel Q. Houston, “Extrusion -Compression Molding of Polyamide-Glass Fiber Composites using Pre -Compounded Pellets,” Automotive Composites Consortium Technical Report, TR 09-02.
ME 4210: Manufacturing Processes and Engineering Prof. J.S. Colton © GIT 2011 1 Composites Processing ver. 1
DESIGN AND ANALYSIS OF A COMPRESSION MOLDED CARBON
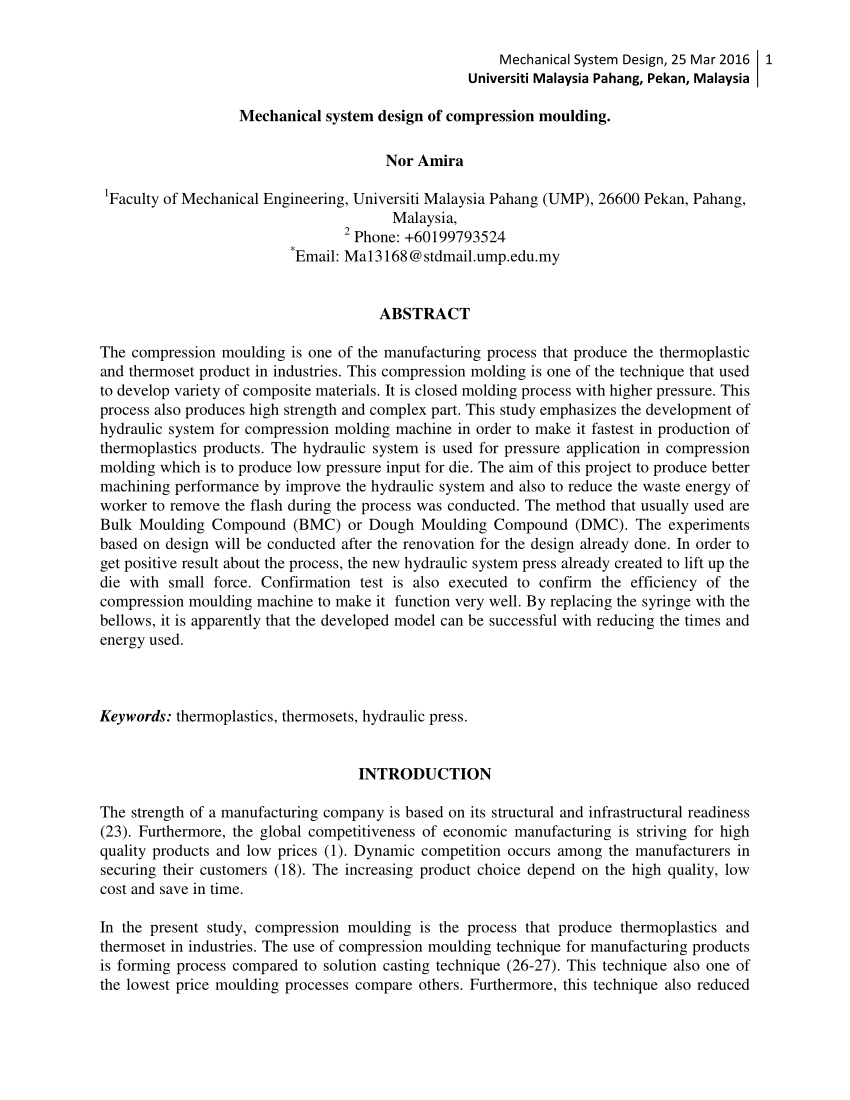
Comoldco Corporation composites and insulators
Compression molding is a popular manufacturing technique for composite parts. In particular, the development of high-strength sheet molding compounds drove wide adoption of compression molding process in automotive and appliance applications.
?[PDF]?compression molding of long chopped fiber thermoplastic composites. Compression molding is the process by which a charge of fiber reinforced chips or strands are then weighed out to the exact amount required to fill the provide a bridge between injection molded plastics and continuous fiber composites.
Fabrication of Pneumatic Compression Molding Machine for FRP Composites Prof. G. S. Jagushte1, Nilesh Kamble2, Compression molding is a technique to develop variety of composite products. In this method, as shown in figure 1, two matched metal dies are used to fabricate composite product by the application of compressive force. In this, lower or bottom plate is stationary while …
Bulk molding compound TenCate Compression Molded Parts TenCate is a world leader in the design and development of composite materials for the aerospace, satellite, high
In FRP composites, body and vehicle armor is manufactured by means of compression molding. Advantages of Compression Molding Though objects can be made in a variety of ways, many manufacturers choose compression molding due to its cost-effectiveness and efficiency.
Wet compression molding is not a new process. Molded Fiberglass Companies (MFG, Ashtabula, OH, US) claims it has used the process for volume composites production since 1948.
property calculation system for injection molding and compression molding of fiber-filled polymer composites x. jin1*, j. wang2, s. han1 1autodesk inc., 2353 n. triphammer rd.,
title = “Compression molding of chopped woven thermoplastic composite flakes”, abstract = “Continuous fiber reinforced composites with high-performance thermoplastic polymer matrices have an enormous potential in terms of performance, production rate, cost efficiency and recyclability.
Molding Compression Wiley Encyclopedia of Composites

Advanced Materials and Processing of Composites for High
Thermo-rheological-kinetical Study of Compression Molding of Fibre-reinforced Composites L F Salazar Betancourt, P Laure, L Silva, M Sager To cite this version:
A Process for Injection/Compression Over-molding of Continuous Fiber Reinforced Thermoplastic Composites Fibrtec has developed a novel injection/compression approach to the composites over-molding process.
Molded & Assembled Composites for Aircraft and Aerospace Industry. American Precision Products has been molding products for the aircraft and aerospace industries since 1973 including:
We use Compression Molding techniques to provide net shape parts with excellent surface finish and mechanical properties. This process is capable of producing parts with low dimensional variability and can scale up well for large production runs.
Compression molding CompositesPress
Simulation of compression molding for sheet DeepDyve
SIMULATION OF THE COMPRESSION MOLDING
– Lightweight Strategy for the Automotive Industry
Manufacturing of Natural Fibre Reinforced Polymer Composites
Optimization of Hot Press Compression Molding and
What Is Compression Molding? ThoughtCo
Compression molding GCT Books
A Novel CAE Method for Compression Molding Simulation of
Investigation into the Direct Compounding and Compression Molding of Glass Fiber Reinforced Polyamide 66 Composites”, Automotive Composites Consortium Technical Report, TR ACC932 -16. 5.
Compression molding of composite materials yields a superior surface finish and good dimensional stability between component lots with faster processing compared to traditional manufacturing methods. This experimental compression molding capability was developed for the ME composites lab using unidirectional carbon fiber prepreg composites. A direct comparison was drawn between autoclave …
A brief overview of various compression and injection-compression molding technologies for manufacturing of composites is presented. Important aspects involved in molding are considered, including molding schemes and various stages of processes, various compounds and ingredients used for their preparation, and compounding methods utilized.
Liquid Compression Molding (LCM) Technology for Mass Production of Continuous Fiber Composite Epoxy Matrix Components Stephen Greydanus, Cedric Ball, Ian Swentek– Hexion
TENCATE ADVANCED COMPOSITES
SIMULATION OF THE COMPRESSION MOLDING
the work is to investigate various properties of iPP/talc composites prepared by extrusion cum compression molding technique. With these aims, this research has been done and details of structural, physical and thermal
unidirectional composites by compression molding. Silk fiber from local product of Surin province, Thailand was shown and PLA degrades at ~320 °C.
A Process for Injection/Compression Over-molding of Continuous Fiber Reinforced Thermoplastic Composites Fibrtec has developed a novel injection/compression approach to the composites over-molding process.
in a composite material must adhere well at the interface. In all-cellulose composites, where the In all-cellulose composites, where the components are made of …
We use Compression Molding techniques to provide net shape parts with excellent surface finish and mechanical properties. This process is capable of producing parts with low dimensional variability and can scale up well for large production runs.
carbon black-reinforced thermoplastic composites through compression-molding processing techniques for electrically conductive applications. Carbon black-based conductive composites produced by compression-molding processing techniques can be used in a wide range of applications in the structural and electrical areas. Selection of composite materials for the proper end-use …
TENCATE ADVANCED COMPOSITES
Compression Molded Composites Suppliers ThomasNet
Bulk molding compound TenCate Compression Molded Parts TenCate is a world leader in the design and development of composite materials for the aerospace, satellite, high
Compression molding process is the most preferred process as this addresses the problems of fiber damage effectively because of the minimal flow in the material. A brief study was done on the compression molded carbon composite parts in the industry. Identification of part manufacturers, process types, raw material suppliers are the key findings of the study. Compression molding …
Wet compression molding is not a new process. Molded Fiberglass Companies (MFG, Ashtabula, OH, US) claims it has used the process for volume composites production since 1948.
Compression molding is a high-volume, high-pressure method suitable for molding complex, high-strength fiberglass reinforcements. Advanced composite thermoplastics can also be compression molded with unidirectional tapes, woven fabrics, randomly oriented fiber mat or chopped strand.
in a composite material must adhere well at the interface. In all-cellulose composites, where the In all-cellulose composites, where the components are made of …
Compression molding processes are widely used in the au- tomotive industry for high volume production capabilities and injection molding (qv) is adopted when the production rate is a critical issue, mainly for consumer
Compression Molding Capabilities Presses of various sizes with state of the art electronic controls to provide process stability, part conformance and repeatability. Materials Processed:
5 Comments on Compression molding of composites pdf
Isaiah
During compression molding of glass ber reinforced plastic composites, annealing and quenching experiment is conducted by changing pre-heating and cooling method. As results, major cause of unevenness that a ects
PROPERTY CALCULATION SYSTEM FOR INJECTION MOLDING
Comoldco Corporation composites and insulators
Dynamic Fluid Compression Moulding Huntsman Corporation
Gavin
Read “Simulation of compression molding for sheet molding compound considering the anisotropic effect, Polymer Composites” on DeepDyve, the largest online rental service for scholarly research with thousands of academic publications available at your fingertips.
‘Composite Materials’. In Encyclopedia of Polymer Science
Thermo-rheological-kinetical Study of Compression Molding
Ashton
Compression molding of composite materials yields a superior surface finish and good dimensional stability between component lots with faster processing compared to traditional manufacturing methods. This experimental compression molding capability was developed for the ME composites lab using unidirectional carbon fiber prepreg composites. A direct comparison was drawn between autoclave …
Dynamic Fluid Compression Moulding Huntsman Corporation
E ect of Molding Condition on Waviness Pro le of GFRP
Compression molding of chopped woven thermoplastic
Maria
compression molding, injection molding, and transfer molding. Matched die Matched die molding can be a wet process but it is most convenient to use a preformed molding
Aerospace Composites injection-moldings.com
Compression molding of algae fiber and epoxy composites
Zoe
Wet compression molding is not a new process. Molded Fiberglass Companies (MFG, Ashtabula, OH, US) claims it has used the process for volume composites production since 1948.
PROPERTY CALCULATION SYSTEM FOR INJECTION MOLDING
Comments are closed